
Additive Manufacturing in a Circular Economy Framework: f3nice Case Study – Giorgio Riccomini
YML Contest for the 2021 WM Report
From March to July 2021, the YML Contest for the 2021 World Manufacturing Report was held, inviting young leaders from all over the world to submit a case study relevant to the topic of Digitally Enabled Circular Manufacturing. The submissions were evaluated by the World Manufacturing Foundation and the winning case studies are included in the publication.
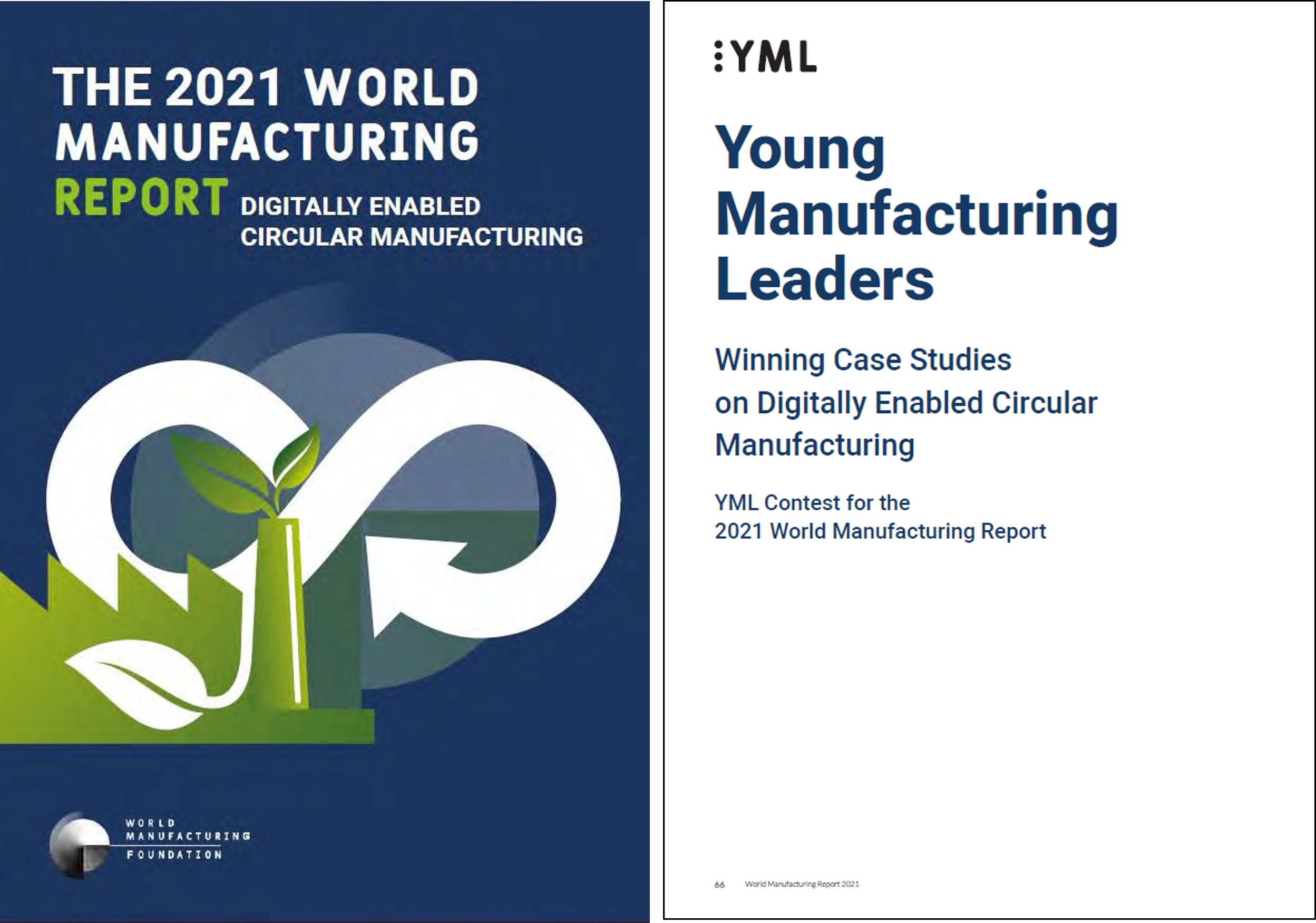
Additive Manufacturing in a Circular Economy Framework: f3nice Case Study
Giorgio Riccomini, Graduate Student at Politecnico di Milano, YML Milan City Hub
Additive Manufacturing (AM) is “the process of joining materials to make parts from 3D model data, usually layer upon layer, as opposed to subtractive manufacturing and formative manufacturing”1 (ASTM F2792). In recent years, the wide availability of CAD software, the increased automation in 3D printing machines thanks to Industry 4.0 digital disruption and major industry and government investment have pushed AM technological development. Additive Manufacturing is cited as one of the key enablers in the transition towards a circular economy (CE) framework2, fulfilling the need for a long-term sustainable perspective.3 CE is a system “restorative and regenerative by design, and aims to keep products, components and materials at their highest utility and value”
As in nature, in a CE framework resources are preserved and balanced, and waste is considered as an added value.4 Opportunities offered by AM are leveraged throughout the value chain. Digital design enables extensive customisation capabilities, shifting production from economy-of-scale to economy-of-one, ending unnecessary stocks3 and possibly extending product lifespan, for instance, by enabling the repair and upgrading of parts.5
AM is paving the way to a “design-based economy”, lowering the barrier between knowledge of the product and the product manufacturing process.3 The design of parts may be augmented by topological optimisation, resulting in a significant weight decrease of the component and in a reduction of physical assembly by merging multiple parts into one. Additionally, significant material savings due to precise material addition and to the absence of tools3 can be obtained, reducing raw material waste.
Lower energy consumption during processing6 and the use of a decentralised economic system by localising the production closer to the end user result in a reduction in the environmental impact of the production process.3 In this context, in May 2020, f3nice, an innovative Italian start-up, was founded with the aim of creating a circular ecosystem for additive manufacturing feedstock production from 100% recycled scrap metal. In January 2021, the start-up raised $120,000 pre-seed funding from TechStars and TechStars Energy Accelerator in Partnership with Equinor. F3nice believes in securing a more sustainable world, by rethinking the traditional industrial production cycles and proposing smart ways to confer additional value to waste. The standard production method for additive manufacturing powder consists in three main phases: raw metal mining, pre-treatment, and atomisation. F3nice, on the other hand, offers an innovative patent-pending solution to produce high-quality powder from scrap metal (e.g. decommissioned valves and obsolete spare parts). Highly valuable metals such as high-alloyed steels, Ni- and Ti-based alloys are recycled to produce green powder in different size ranges, either for Additive Manufacturing or conventional powder-based processes. The expected impact of the project in terms of sustainability can be explained by the words of Matteo Vanazzi (co-founder and CTO of f3nice): “The major sustainability impact derives from the patent-pending powder production process employed, that uses 100% recycled material.
Metal recycling is a generally diffused practice; in any case, it is not usually employed in a 1:1 ratio, rather, a refinement of the composition of the alloy is made by adding pure raw material from mining extraction. Therefore, in standard alloys it is difficult for the percentage of recycled materials to exceed 60%-80%. Through the accurate selection of scrap material and the patent-pending process, on the contrary, f3nice can produce metal powder with the finest quality with 100% recycled material. This will impact significantly on the energy savings of the process. Compared to a traditional production process, estimated savings range from 40% to 70%, depending on the specific alloys.
An evaluation of CO2 emissions reduction strongly depends on the energy mix considered. Localising the innovative powder production process in zones characterised by a favourable energy mix (100% renewable energy), it is possible to obtain savings of up to 90% compared to a standard European energy mix (e.g. in Italy, the UK or Germany), where most powder production takes place today.”
It is important to emphasise that a study is under way at the Politecnico di Milano Department of Energy Engineering to validate all these estimations. The challenge f3nice has taken on is remarkable, since the goal is to establish a business that is innovative, sustainable, and, at the same time, economically successful.
In an interview, Luisa Mondora, CEO of f3nice, shared the major issues that the company has faced during the start-up period: “Primarily, it was very difficult to dispel the doubts of potential clients with regard to the quality of a product coming from recycled materials”. In terms of performance and part quality, the multiphysics nature of the AM process results in high sensitivity to the powder related parameters: particle shape, size and distribution. “Before connecting with main investors”, affirms Luisa Mondora, “we self-funded two proofs of concept, one at laboratory scale and another at industrial scale, to demonstrate that powder produced with our process has comparable or even better quality than powders obtained from raw material mining currently available on the market”. F3nice is able to count on the great support of AIDRO Hydraulics and 3D printing, one of the company leaders in the AM European landscape led by the CEO, Valeria Tirelli, for the production and qualification of parts realised with 100% recycled green powder.
In conclusion, Additive Manufacturing technology fits perfectly into the circular economy framework. Digital design and part optimisation enables unmatched production flexibility with reduced energy and material consumption. Great environmental benefits are made possible by the strategic decentralisation of economic systems and the more customer-oriented demand manufacturing.3
In this dynamic landscape, f3nice is paving the way to a more sustainable production of feedstock powder for additive manufacturing, providing cross-cutting competences in terms of material science and process engineering. The circular flow is finally closed, giving new value to scrap metal, to create high-quality powder for high-performance parts.
References
- International Standard ISO/ASTM52900-15. (2015). Standard Terminology for Additive Manufacturing – General Principles – Terminology. ASTM International, West Conshohocken.
- Spaltini, M., Poletti, A., Acerbi, F., Taisch, M. (2021). A quantitative framework for Industry 4.0 enabled Circular Economy. Procedia CIRP, 98, 115–120. Retrieved from: https://doi.org/10.1016/j.procir.2021.01.015
- Angioletti, C. M., Sisca, F. G., Luglietti, R., Taisch, M., Rocca, R. (2016). Additive Manufacturing as an opportunity forsupporting sustainability through implementation of circular economies. Proceedings of the Summer School Francesco Turco.
- Ellen MacArthur Foundation. (2013). Toward the Circular Economy: Economic and business rationale for an accelerated transition, pp. 1–97.
- Sauerwein, M., Zlopasa, J., Doubrovski, Z., Bakker, C., & Balkenende, R. (2020). Reprintable Paste-Based Materials for Additive Manufacturing in a Circular Economy. Sustainability (Switzerland), 12(19), 1–15. Retrieved from: https://doi.org/10.3390/su12198032
- Khalid, M., Peng, Q. (2021). Sustainability and Environmental Impact of Additive Manufacturing: A Literature Review. Computer-Aided Design and Applications. 18(6), 1210–1232. Retrieved from: https://doi.org/10.14733/cadaps.2021.1210-1232