
Circularity Enabled by Additive Manufacturing: a General Electric Case Study – Kateřina Kobrlová
YML Contest for the 2021 WM Report
From March to July 2021, the YML Contest for the 2021 World Manufacturing Report was held, inviting young leaders from all over the world to submit a case study relevant to the topic of Digitally Enabled Circular Manufacturing. The submissions were evaluated by the World Manufacturing Foundation and the winning case studies are included in the publication.
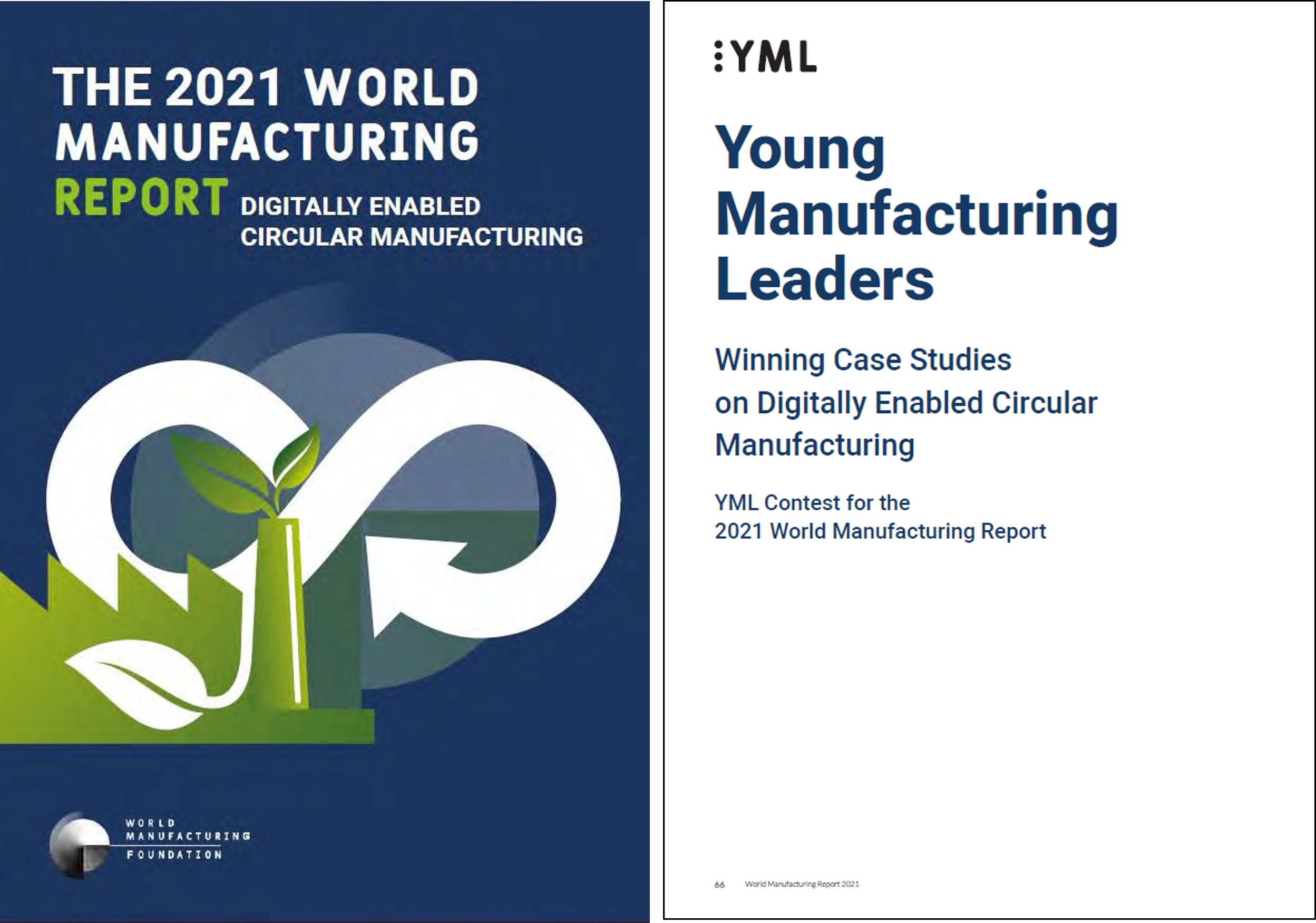
Circularity Enabled by Additive Manufacturing: a General Electric Case Study
Kateřina Kobrlová Master’s Degree Student, Czech Technical University in Prague – YML Prague City Hub
As one of the world leaders in the industrial sector, General Electric (GE) has shown an increased interest in the use of additive technology in the aerospace sector for more than a decade. GE Aviation, as a part of a multinational conglomerate, plays a crucial role in producing lightweight and durable components with complex geometry. Additive Manufacturing (AM), with the main focus on 3D Printing (3DP), is a manufacturing method which allows the creation of parts with specified parameters but also effectively reduces production time and fuel consumption in comparison to traditional components.1
Digital solutions like AM with 3DP will allow the local market to be supported and the country or continent will become less dependent on imports of scarce raw materials. 3DP is essential for a circular economy (CE) as it is resilient to supply chain disruptions and as it uses less material than traditional production. CE promotes a smaller environmental footprint, enhances the development of a sustainable business model, and represents systems that reuse, recycle, and recover materials, and seeks a more efficient use of resources. These objectives are supported by AM and 3DP since they aim to accomplish environmental quality and prosperity for future generations.2, 3
GE seeks to examine the nature of AM and raise awareness for its use in aviation. To do this, GE needed to investigate a comparison of traditional manufacturing techniques and AM processes. Since the 1990s, 3DP has attracted a lot of interest, while GE Aviation has been working closely with Morris Technologies to print prototypes of newly designed engine parts. They set out to investigate the usefulness of lasers for welding thin layers of a metal powder to print nozzle tips from a nickel alloy. The parts were combined into a single unit which weighed less, and the final product was more durable than a conventionally manufactured nozzle tip. This has led to the establishment of a solution that would avoid the use of bolts, welds, or nuts, but also provides a path to cost reduction and enables fuel burn to be improved by 20%. GE has also reduced development time by a third while using rapid prototyping that systematically reviews product data at the start of the design process, thus allowing improvements at an early stage of the process.1,4 The additional objective of the project focused on AM intended to determine the extent to which GE can replace parts that may no longer be produced by supply chains in the future. Only a few suppliers invest in the aerospace sector. GE needed to examine options that could help avoid being affected by the cost models of other businesses and which would not reduce the speed of production.5
To take metal additives into full-scale production, GE delivers innovation by utilising Direct Metal Laser Melting (DMLM) machines. The Concept Laser M2 Series 5 printer is intended for serial production and allows us to create thinner walled structures using materials such as stainless steel, aluminium, nickel, titanium, and cobalt.6, 7 Another advanced solution is offered by the M Line Factory machine, with a separated process and handling unit. It suppresses the secondary times in the AM process, such as removing parts and setting up a machine for another process, and it prevents delays in production.8
In 2014, GE announced plans to invest $50 million in GE Aviation in Auburn to prepare the facility for AM. They began producing fuel nozzle tips and reached production of 30,000 additive nozzles for CFM International’s LEAP engine.
The original nozzle tip had about 20 pieces and the number of parts was reduced to one whole piece, reducing the weight by about 25%. It also led to the production of five times more durable parts with a 30% cost efficiency improvement. This example leads to the use of AM in mass production in aviation.9
Previous research and attempts have helped establish the development of the GE Catalyst turboprop engine that consisted of more than 800 conventionally produced parts, recreating it using only 12 components. A similar strategy was utilised for the GE9X engine, which combines more than 300 conventional parts; this was reconceived so that it needed only 7 printed parts. By 2020, the company had identified more than 80 additional components that could be reworked with 3DP. In 2019, GE Aviation and GE. Additive began working with the U.S. Air Force (USAF) to find faster production of spare parts to replace damaged parts. The first project investigated the utilisation of AM for a F110 engine sump cover, which is used in F-15 and F-16 aircraft. The sump cover can be considered less functional in a complex engine, but it is a very important part that must meet several conditions, such as durability and rigidity. The main reason for starting to think about the use of AM in the USAF were difficulties with suppliers and the long delivery times, which are approximately 2-3 years. The implementation of the plan has begun with searching for simple parts and then transitioning to complex systems. The M2 machine was used for the first production of the F110 sump cover, after which the engineering team’s focus shifted to the recreation of the 40-year-old TF34 engine sump.10, 11
AM brings great value to the market and indicates the need to understand and overcome various challenges, e.g., the temperature inside the jet engine exceeds 1300 degrees Celsius, and we must learn how the AM can cut costs and support repairs in such conditions. GE has made investments in technology and development and has begun to take AM to the next level by sharing the know-how with its units.1 M.Eng. Vít Havránek, Product Definition Lead Engineer and Designer of Additive Components at GE Aviation Czech, states, “The last two years of the additive design sector have been focused mainly on cooperation with the European Space Agency (ESA) and Brno University of Technology (VUT). We are trying to convert conventional components from the engine of the GE H-Series into additively manufactured parts. To make sure that we achieved the expected goals, parts manufactured by conventional production methods and AM production parts were compared in order to determine the influence of additive methods on assembly, compare strength analysis and evaluate the achieved accuracy of newly designed components.”
References
1 AirForce Magazine. (2020, May 15). GE Wants to Bring the Speed of Additive Manufacturing to the Air Force. Retrieved from: https://www.airforcemag.com/gewants-to-bring-the-speed-of-additive-manufacturing-to-the-air-force/
2 Urbinati, A., Rosa, P., Sassanelli, C., Chiaroni, D., Terzi, S. (2020, July 18). Circular business models in the European manufacturing industry: A multiple case study analysis. Journal of Cleaner Production, 274. Retrieved from: https://doi. org/10.1016/j.jclepro.2020.122964
3 Hedberg, A., Šipka, S. (2020, July 13). Towards a green, competitive and resilient EU economy: How can digitalisation help? Retrieved from: https://www.epc.eu/content/ PDF/2020/Towards_a_green_competitive_and_resilient_EU_economy.pdf
4 Twi. (n.d). What is Rapid Prototyping? – definition, methods and advantages. Retrieved from: https://www.twi-global.com/technical-knowledge/faqs/faq-manufacturingwhat-is-rapid-prototyping
5 Madeleine, P. (2021, May 10). GE Aviation Switches to Metal AM for Four Parts, Cutting Costs by 35%. Retrieved from: https://www.3dnatives.com/en/ge-switchesto-metal-am-for-four-parts-100520216/
6 Cad.CZ. (2019, November 29). GE Additive představuje nové tiskárny pro 3D tisk kovů. Retrieved from: https://www.cad.cz/aktuality/77-aktuality/10002-ge-additivepredstavuje-nove-tiskarny-pro-3d-tisk-kovu.html
7 GE Additive. (2020). For the ready. Take to the skies with proven metal additive solutions. Retrieved from: https://www.ge.com/additive/industry/aerospace?utm_ campaign=&utm_medium=organic+social&utm_source=twitter
8 Misan s.r.o. (2020, August 7). Pokroky ve 3D tisku z kovových prášků od GE. Portál profesionálů strojirenstvi.cz. Retrieved from: https://www.strojirenstvi.cz/pokroky-ve3d-tisku-z-kovovych-prasku-od-ge 9 GE Additive. (2018, October 4). New manufacturing milestone: 30,000 additive fuel nozzles. Retrieved from https://www.ge.com/additive/stories/new-manufacturingmilestone-30000-additive-fuel-nozzles
10 Misan s.r.o. (2020, August 10). U.S. Air Force a GE spolupracují na aditivní výrobě olejové vany pro motor F110. Retrieved from http://okamoto.cz/clanky/2020-08-10- us-air-force-a-ge-spolupracuji-na-aditivni-vyrobe-olejove-vany-pro-motor-f110/
11 Koenig, B. (2020, January 29). 3D Printing Cleared for Takeoff. Retrieved from: https://www.sme.org/technologies/articles/2020/january/3d-printing-cleared-fortakeoff/