
Digital Technology for the Recycling of Waste in the Steel Sector – Elena Fernández Calvo
YML Contest for the 2021 WM Report
From March to July 2021, the YML Contest for the 2021 World Manufacturing Report was held, inviting young leaders from all over the world to submit a case study relevant to the topic of Digitally Enabled Circular Manufacturing. The submissions were evaluated by the World Manufacturing Foundation and the winning case studies are included in the publication.
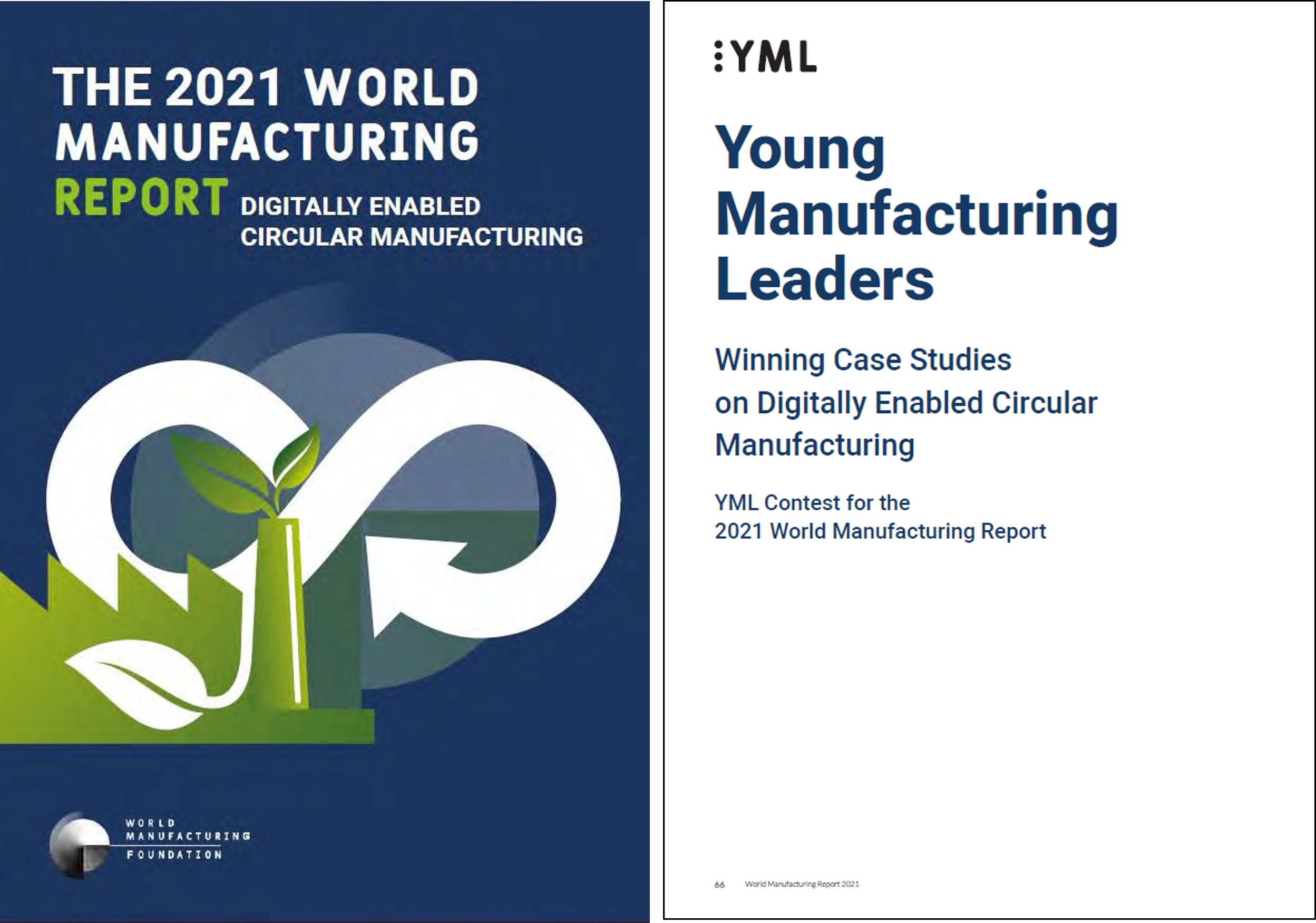
Digital Technology for the Recycling of Waste in the Steel Sector
Elena Fernández Calvo Bachelor’s Degree Student, IMH University – YML Basque City Hub
Nowadays, companies are increasingly introducing digital technologies in order to solve different problems in their production and also, to be more environmentally sustainable. This project will be focused on the steel industry, specifically in a factory that produces cut taps. The problems that the company have are the difficulties in recycling the emulsion waste and also the steel chip waste. Once the emulsion is used, it is adulterated by steel chip from the taps, dust from the cutting wheels and different oils and lubricants. With these problems, the project will consist in proposing a solution for the reuse of waste for the purposes of being more sustainable and also to obtain benefits.
There are different types of waste but in general, those which may cause more problems within the steel industry are emulsion and steel chip waste. Government policy requires companies to have strict control of the waste that they produce in order to reduce world pollution levels. This means that there is an urgent need for manufacturers to be more eco-friendly so that it is possible to meet the standards that climate change laws demand of industries with a view to decreasing their impact on Earth’s global warming.
In the first place, one of the problems is emulsion waste. Emulsion is used in the machines to aid their processes, which makes it a very important component of factory production. The composition of emulsion is oil (approximately 5%) and water (around 95%), depending on its uses. Besides, the initial properties start disappearing when it is used and instead of oil and water, the emulsion starts to assimilate other oils, steel waste and dust wheel. This combination between different outside factors and the emulsion becomes a highly polluting waste product, so factories need to find a solution to recycle or reuse it. For the time being, there is no perfect solution for emulsion waste but by using digital technologies, factories can start controlling the amount of different waste in the initial emulsion and they can also reuse it. Taking advantage of digital technologies, factories can be furnished with digitalised emulsion filters. These filters have sensors that send various data to a computer. They send data relating to the amount of non-liquid particles so that the oil and water can be separated from the dust and steel chip, and also, once separated, the sensors send the information about the percentages of oil and water. If the levels of oil and water are acceptable (these values are established by the supplier and the factory), the emulsion can be filtered by adding a barrier through which only the emulsion that is going to be reused can pass. The oil that can no longer be used can be converted into fuel.
On the other hand, the factory has two types of steel chip waste, that which the machines generate while they are grinding the taps and that which is obtained when they filter the emulsion.
One of the problems in both situations is that the steel chip is in continuous contact with the emulsion, in particular that which is accumulated in the filter. This means that before the company can recycle or reuse it, the chip has to go through a cleaning and drying process. Once the chip is free of emulsion, there are different options regarding its use. The most environmentally sustainable may be reusing the oil obtained from the emulsion as fuel for heat, or melting the steel in furnaces at different temperatures. The problem with the steel waste in this factory is that they work with M2 and ASP23 steel and both of these have a high melting point. For this reason, melting the steel requires a specific furnace.
Currently, the factory sells the steel waste instead of recycling or reusing it. In order to have a circular economy and also to be more eco-friendly, the proposal in this case is to install a specific furnace in the heat treatments area which has the capability of raising the melting point of each material. As is known, it is not an easy job to obtain a furnace with these characteristics, so the process can be split into two phases. The first heats the steel to a defined temperature; for this process, the company can reuse the current furnaces and recondition them by adding sensors that will send different types of data (temperature, durability, errors, etc.) to a computer. In this phase, the fuel that it is needed will be obtained from the emulsion. Once the steel reaches the desired temperature it will be moved to the other furnace. This other furnace will also have different sensors to store all the data in a computer and will be able to analyse it. In this second phase, the steel will be completely melted so that it can be reused for different applications by giving it the desired shape.
The main advantage of using this technology is that by reusing the emulsion and the steel chip there will be less pollution, which means that the environment will be more sustainable and so global warming will be decreased. A further advantage is that despite the expense that can be generated by the digitalised emulsion filters and the digitalised furnace, the factory will increase earnings in the long term by reusing the waste because they will have a closed circuit that distributes, filters and reuses the emulsion and also harnesses the steel.
To conclude with the advantages, there is that of having all the information about the emulsion and the steel chip process digitalised, which allows the company to store all the data in a computer. They can use this data to decide how long the reuse of the emulsion is viable and when more will need to be ordered, to monitor the levels of pollution in the emulsion, and so on. In addition to these advantages, there are some disadvantages. In economic terms, one of the main disadvantages is that to install the digitalised filters and the digitalised furnace in the factory, they will have to make an initial outlay that not all the companies are willing to do. Another point is that the design of the sensors has to be precise and that is arduous work because they will have to be exposed to high temperatures, so the material of which they are made must be high-temperature resistant.
To conclude, factories need to reconvert their processes into a sustainable, non-contaminated production system as soon as they can, in order to decrease global warming. By reusing the waste that this type of factory generates, it will become more eco-friendly and will also make money in the long term. Manifestly, to get to this point, companies will need to make a high initial outlay and most of them are unwilling to do so. If governments finance a part of these projects, therefore, in the coming years factories will become more sustainable because they will reuse their own waste as illustrated in this case.
Figure 1. Illustration of Processes
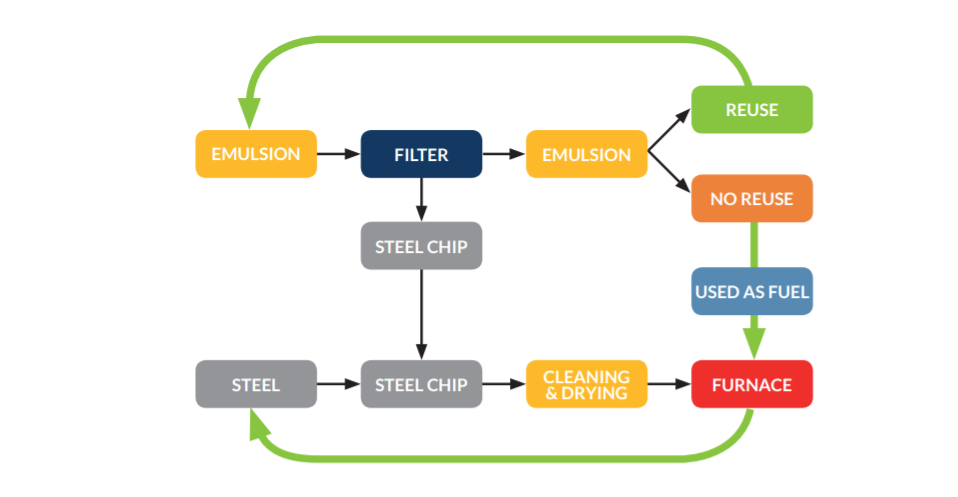